ok, take a look at these |
I have been sent some interesting locks thet need some repair, I thought maybe it would give us something to chat about. Let me know what yoou think of them...
Barry Lee Hands
11/26/2005 8:28:12 PM

![]()
![]()
![]()
|
Nice locks Barry. What do they want you to do to them? Also..what type of camera did you use to photograph them? they look pretty clear
Martin Rabeno
11/27/2005 9:47:13 AM

![]()
![]()
![]()
|
Hi Marty, long time no see my friend, nice to hear from you. You may notice there is a piece of tape holding whats left of the #1 duck on the right lock in place. It came in for repair. I scanned the locks on an epson 4870 photoscanner,at about 1200 dpi then cropped, enhanced and reduced the size a little so they would not be too huge....There is a lot of history and a long story behind these, but I do not know all of it, I am hoping someone might know more of it.
Barry Lee
Barry Lee Hands
11/27/2005 11:56:08 AM

![]()
![]()
![]()
|
So, Barry,how long you figure before the rest of the inlays fall out? Sam
Sam Welch
11/28/2005 1:53:49 PM

![]()
![]()
![]()
|
Barry, it appears as though there is an engravers mark just below the scotch tape. Could be K Hunt from what I can tell without a magnifier. Just wondering if it was. Mike
Mike Bissell
11/28/2005 6:16:13 PM

![]()
![]()
![]()
|
Hi Barry, will you let us know if the inlays are sheet or constructed wire, please?
Mike, I an almost sure the mark is K. Hunt '56.
Thanks for posting this interesting project, Barry.
Very best wishes to you.
John
John Barraclough
11/28/2005 7:21:05 PM

![]()
![]()
![]()
|
Hi Sam, the rest of them are in reasonable shape. I think there were some burrs poking through when it was first done which allowed water to seep in and caused rust which pushed up the inlay, or it may have been polished during one of its many refurbishments, causing the burr problem.
Mike,the mark is K. Hunt.
David Trevallion is researching this, the beginning of the story at this point is this was done by Hunt, at Kell's shop on Broadwick street in London, while he was still an aprentice.
John,It seem to be a constructed wire Inlay, and there are burrs and an undercut around the edge.
I will restore it with the minimal disturbance, stabilizing the loose gold and leaving the rest.
The left hand lock is fine, does anyone have any observations on it?
Here is a closeup of the cavity on the right lock..
Barry Lee Hands
11/28/2005 7:46:02 PM
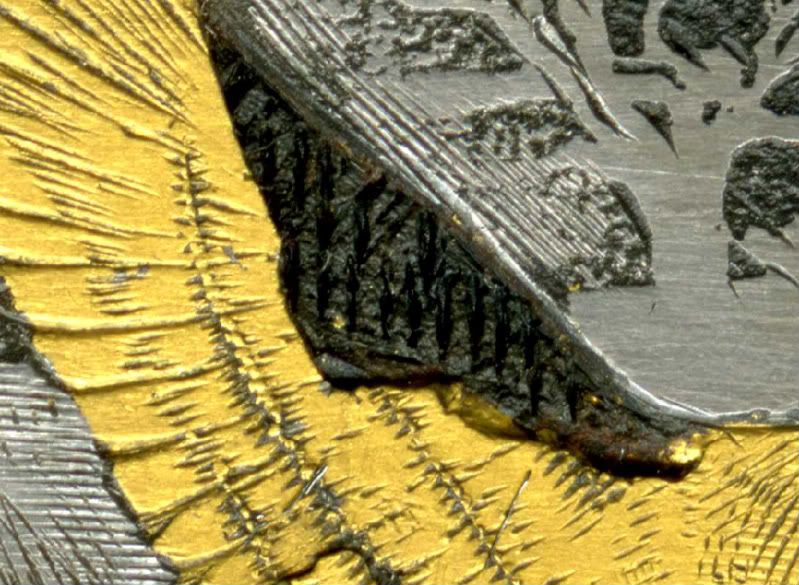
![]()
![]()
![]()
|
John Vukos
11/28/2005 8:01:25 PM

![]()
![]()
![]()
|
re. left side - spelling
John Vukos
11/28/2005 8:01:56 PM

![]()
![]()
![]()
|
Barry, is it the photo or is there a lot of steel bits showing through the gold? Also, as John Vukos notes, the "R" on the left side looks more like a "U". Is that also the photo or is it a "U"? I don't envy you the repair job!
Sam Welch
11/28/2005 10:37:17 PM

![]()
![]()
![]()
|
Barry,
Thank you for the information about the composition of the inlays and your work in
posting this most interesting project.
The most difficult part that I have found in this type of repair is in creating a new, sharp burr field in the already somewhat overworked steel.
With the help of a microscope and you fine skill, I know you will make a wonderful job of it. Please post a photograph of it when you complete it.
I think it’s a wonderful example of Ken Hunt’s early work and quite remarkable considering the short amount of time and low pay that the engravers were allowed in 1956, especially when you were an apprentice. I believe Mr. Hunt was still an apprentice in Harry Kell’s shop at this time and of course, most of the work was done standing, with a hammer and chisel and without the benefit of great lighting and a microscope.
The scroll work is very well done in a traditional mode, and still looks wonderful 50 years down the road.
Thank you for this most interesting post, Barry. Hope to see you in Reno. Maybe you will have the sideplates there.
John Barraclough
11/29/2005 12:22:27 PM

![]()
![]()
![]()
|
Thanks for the great comments everyone.The R is an R it just looks funny because of the lighting. And the left lock is a different engraver, any guesses? I hope we are having fun with this. The repair is underway and I have pics if you wish to see them. This pic is shows that I have protected the surface with rebite ground, in preparation of etching out the rust with acid.
Barry Lee Hands
11/29/2005 2:59:45 PM
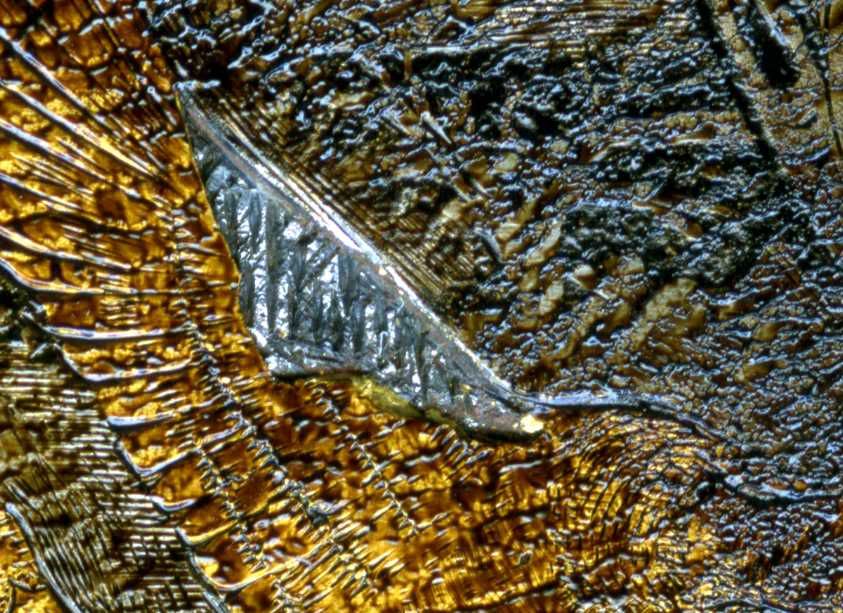
![]()
![]()
![]()
|
oh, and yes Sam those are bits of steel poking through. That may be one way the moisture got in there in the first place, There is also some steel wool lint floating around on the surface..B
Barry Lee Hands
11/29/2005 4:31:46 PM

![]()
![]()
![]()
|
Lynton McKenzie?
/
Fred Marrinan
11/30/2005 7:51:42 AM

![]()
![]()
![]()
|
After etching the cavity I got to poking around and pulled this up...I call this pic "duck wing shredded" So I did the same operation in here.
Barry Lee Hands
11/30/2005 12:19:30 PM
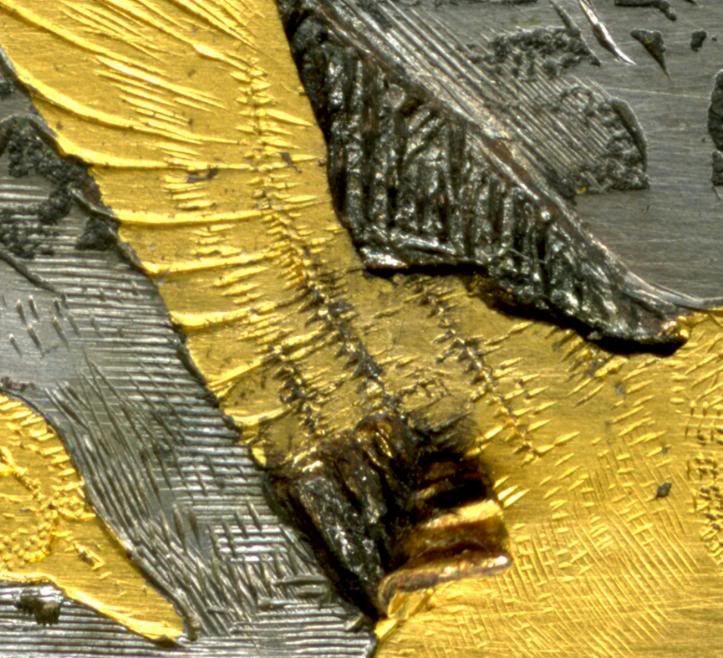
![]()
![]()
![]()
|
Fred, you are correct,good work, thank you for the observation.
Barry Lee Hands
11/30/2005 12:37:01 PM

![]()
![]()
![]()
|
I have been thinking (dangerous game to play) and it seems to me all the inlays on this side plate are very suspect. I don't see how that much corrosion formed just because there was steel sticking through the gold. Unless the gold was not that firmly seated. 1956, hot and humid England,no air...there are other possiblilies along the way if the gold was loose at all. I would be tempted to pull some gold around that second area to see how far the corrosion extends. Completely redoing the inlays would seem prudent, though expensive and time consuming.
Sam Welch
12/1/2005 8:42:43 AM

![]()
![]()
![]()
|
Yes Sam, good point, and I am sure there is some corrosion in other places. To stop further corrosion in the immediate future, I boiled it.I have poked around quite a bit and nothing else is actually loose.I tested with carpet tape also.The client wants to preserve as much of the original work as possible, and I think this is a good idea. This gun has a lot of history, David Trevallion has told me he thinks that it has had over 100,000 rounds through it live pidgeon shooting. And the current owner uses it heavily. If any more falls out later, we can fix more later. If you though that pic was ugly, you will hate this one. Thanks for the observations. Barry
Barry Lee Hands
12/1/2005 11:09:08 AM

![]()
![]()
![]()
|
Barry, I agree with Sam's last posting. I had thought all along that all the inlays on that side were suspect, but the damaged one at least, needed to be totally redone. I just hated to say it and be a wet blanket, know-it-all.
Personally, knowing the number of KH inlays that have had similar problems, I tend to think it's in the way that Ken goes about it. Maybe very acidic hands or gold contaminated by flux and not completely cleaned. Or gold annealed by heat and quenched in Sparex, as the jewelry trade does.
The clue is.... Lynton's side held up under the same conditions. KH's have sometimes had problems on both sides of the gun, when he had done the whole gun. That's why I think it might be contaminated gold. As we know, with two different metals in contact with acid, you've got a battery and rust on the ferrous metal.
Just a thought. John
John Barraclough
12/1/2005 11:33:40 AM

![]()
![]()
![]()
|
Here is the next stage, wire trimmed, flattened a little, with a line cut between it and the old metal, so it will have a tight seam when flattened completely.
Barry Lee Hands
12/1/2005 12:08:55 PM
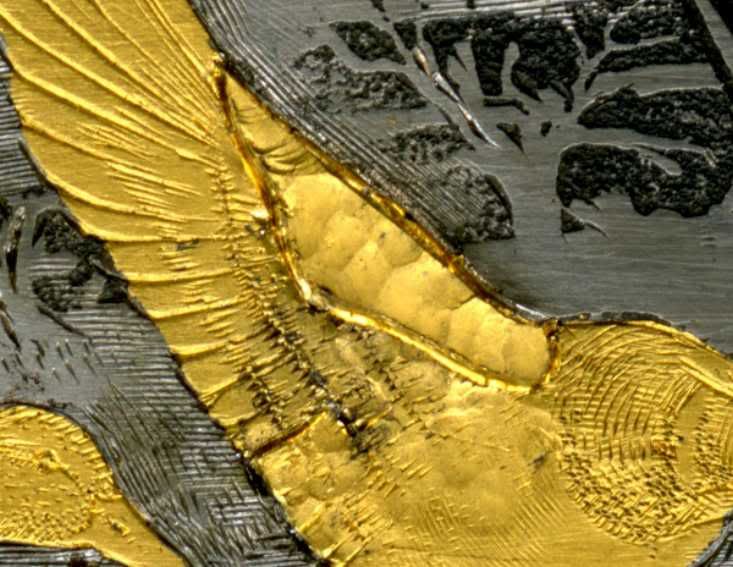
![]()
![]()
![]()
|
now it has been punched down, and is being stoned.
Barry Lee Hands
12/1/2005 12:30:27 PM
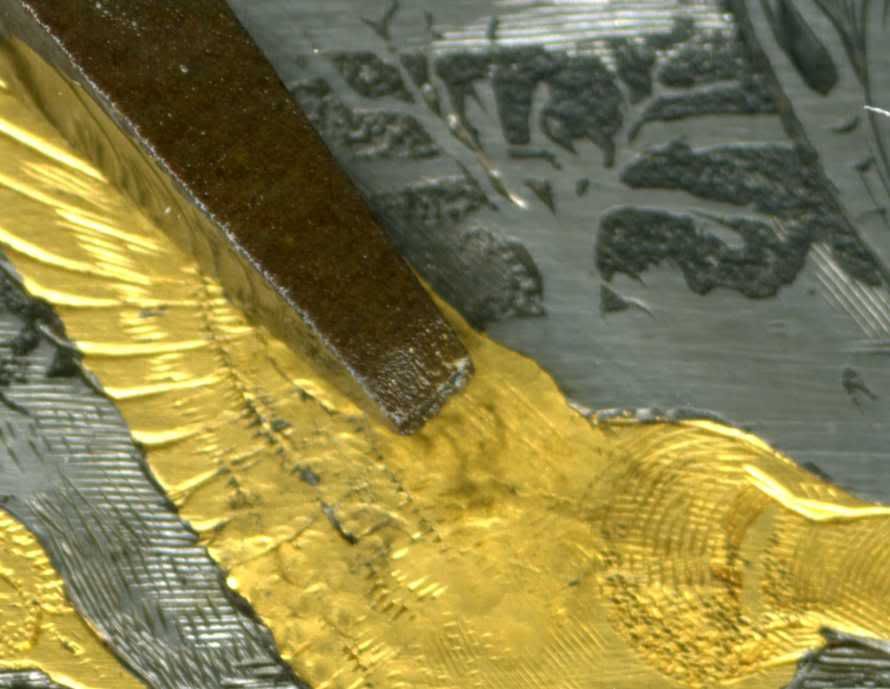
![]()
![]()
![]()
|
Next I cut a channel through some of the steel poking through and raise teeth to recieve a wire.
Barry Lee Hands
12/1/2005 12:32:47 PM
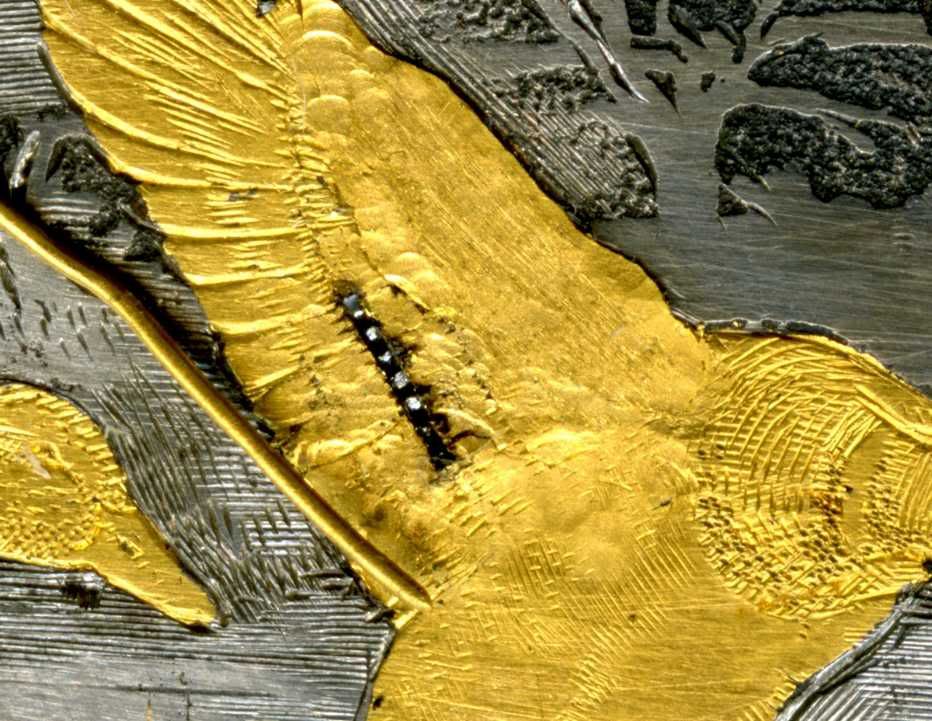
![]()
![]()
![]()
|
the wire is installed, the area stoned,
Barry Lee Hands
12/1/2005 12:35:32 PM
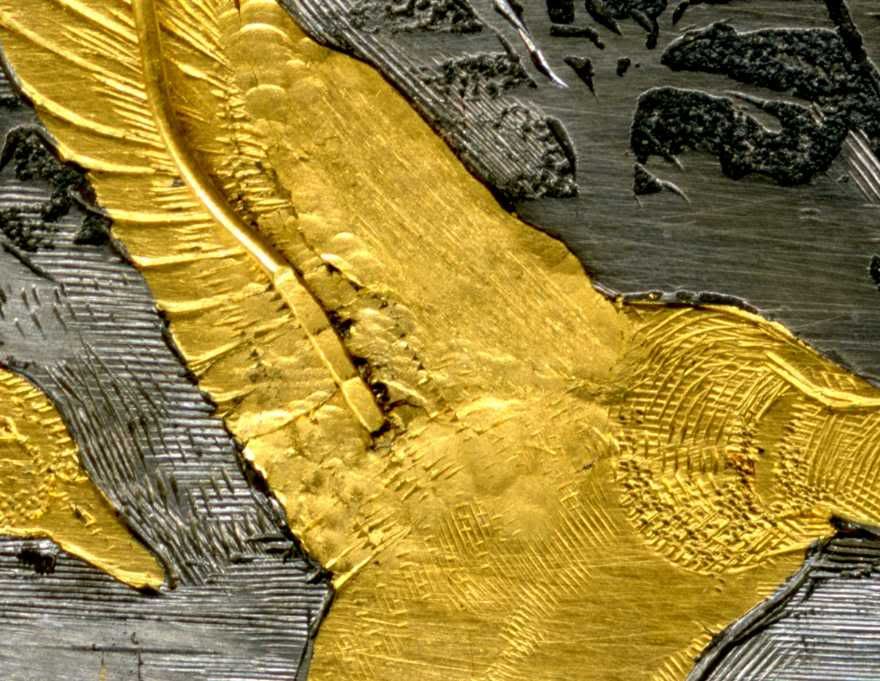
![]()
![]()
![]()
|
and the detail is put back in.
Barry Lee Hands
12/1/2005 12:37:47 PM
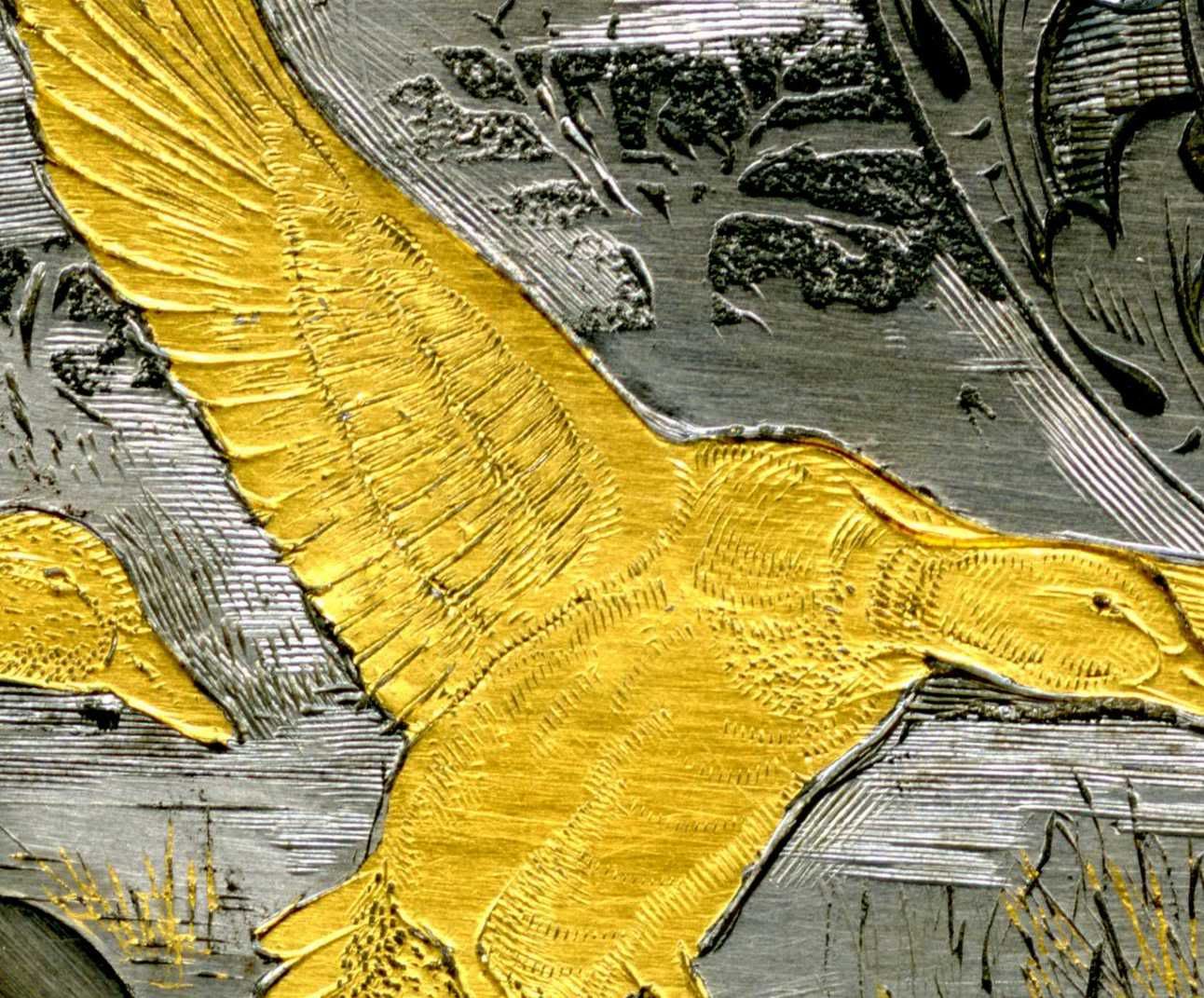
![]()
![]()
![]()
|
And the locks are cleaned, and returned to the client.
Barry Lee Hands
12/1/2005 12:42:16 PM
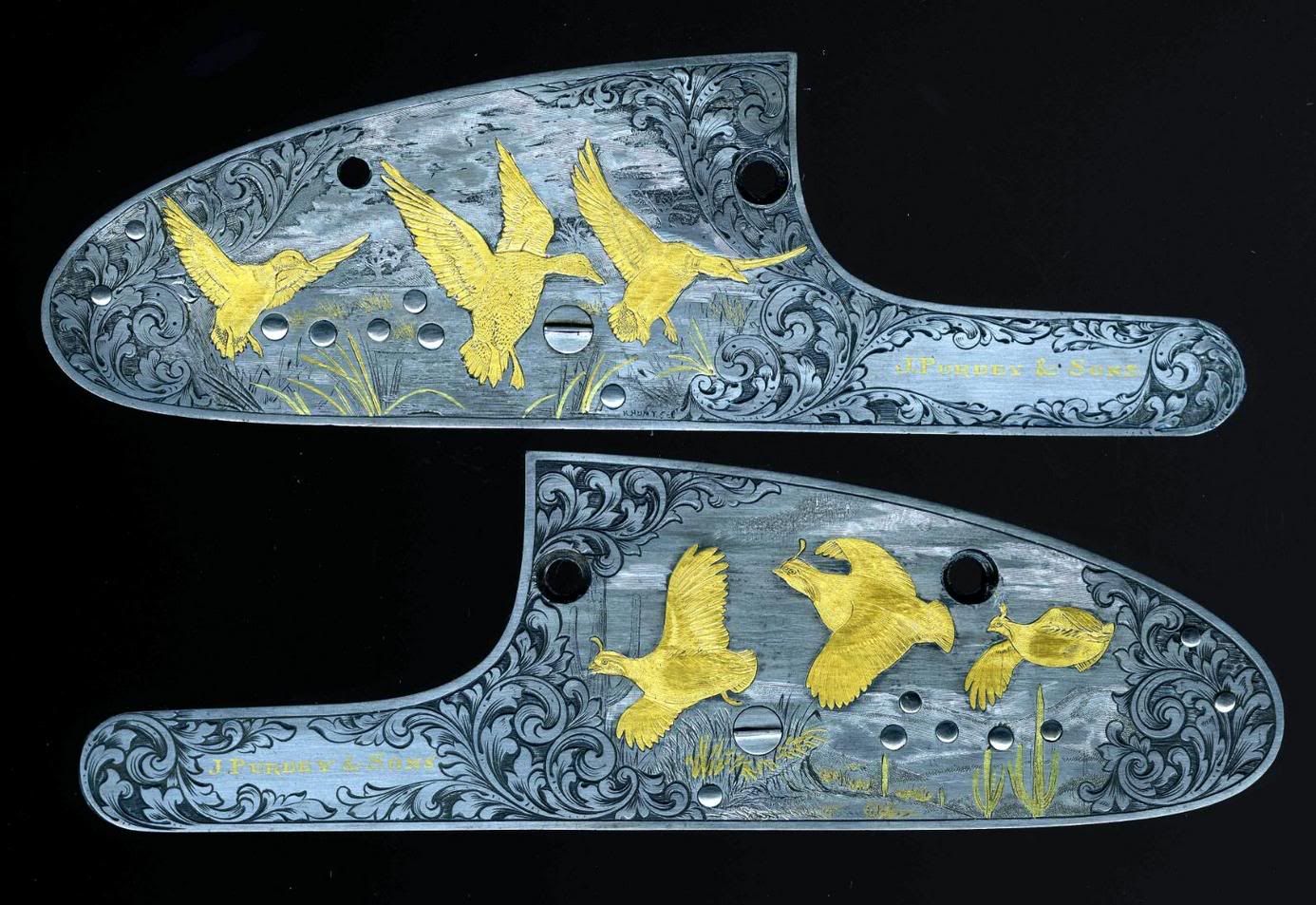
![]()
![]()
![]()
|
Excellent job Barry. When you said you "boiled" the piece just what did you mean? Do you plan to do the wire repair on areas of the other inlay showing a lot of steel? I had assumed the gun had been used a lot. The last time I talked with Frank Hendricks I asked what he was working on and he said he was repairing some gold inlays and that he had done several of these jobs...all KH. S
Sam Welch
12/1/2005 1:25:56 PM

![]()
![]()
![]()
|
Thanks Sam. When I said "boil" it, I meant just that, in water. I don't know why, but it tuns red rust into black rust which is resistant to rerusting. I then blew it dry, wrapped it in paper towels and buried it in silaca gel for a day, this sucks them moisture out pretty well. Now that the repair is done I will post some interesting closeups of the work soon. I can't speak for KH, but I am posting something I emailed to john where I paraphrase what he told me when I mentioned his work is critisized for being thin etc. and I explain this posting.
Email to John:
"The point here is to stabilize an historic gun, not to get every rust pocket out that can be found. The gun spent most of its life in texas shooting live pidgeon, and the Lynton work was done almost 20 years after the gun was shipped, and after most of the use. I am not going to tear out a bunch of inlays that show no sign of being loose by Ken Hunt's hand just cuz it can be done "better". I am not posting this to show how good I am at resto's, but because I think it is a very interested piece, and I am genuinely interested in Sam's, yours and anyone else's, novice, or expert opinion. And mainly because the posting seems slow on the forum, and I wanted to see if this would get more people going.
That was why I started this thread.
Was Lynton more thorough? of course. He also died fairly poor from a stress related illness, while Ken Hunt, an older man, is amongst the oldest, and happiest, most respected and wealthiest engravers, living today. And, he may have had a few fall out, but he has had more stay in than most engravers inlay in their lifetime. If you judge him by his body of work, no one else comes close. In my humble opinion.
I asked Ken about the thin inlays and use of damascening verses using thick material and an undercut and the critisisms of his works' durability. If I may sum up my impressions, and paraphrase: He says he knows he could make them more secure, but his clients are interested in the best Art he can create, not whether it will last a thousand years, and he enjoys pushing the techniques to the limit, his work is limited by a budget, the clients want to see lots of gold, and good enough is good enough.
.
Lynton studied under Hunt, Just as Einstein studied Maxwell and Planck...one hopes a good student can improve on the teachings of those before him, some do, some don't.
Thanks again my friend for your thoughts,
Sincerely,
Barry Lee Hands"
Barry Lee Hands
12/1/2005 2:07:40 PM

![]()
![]()
![]()
|
Here is a closeup, the color is not so good, but he was using yellow and green gold together all the way back in 55 or 56
Barry Lee Hands
12/1/2005 2:15:14 PM

![]()
![]()
![]()
|
Here is a closeup, the color is not so good, but I thought it was interesting that he was using yellow and green gold together all the way back in 55 or 56
Barry Lee Hands
12/1/2005 2:16:03 PM
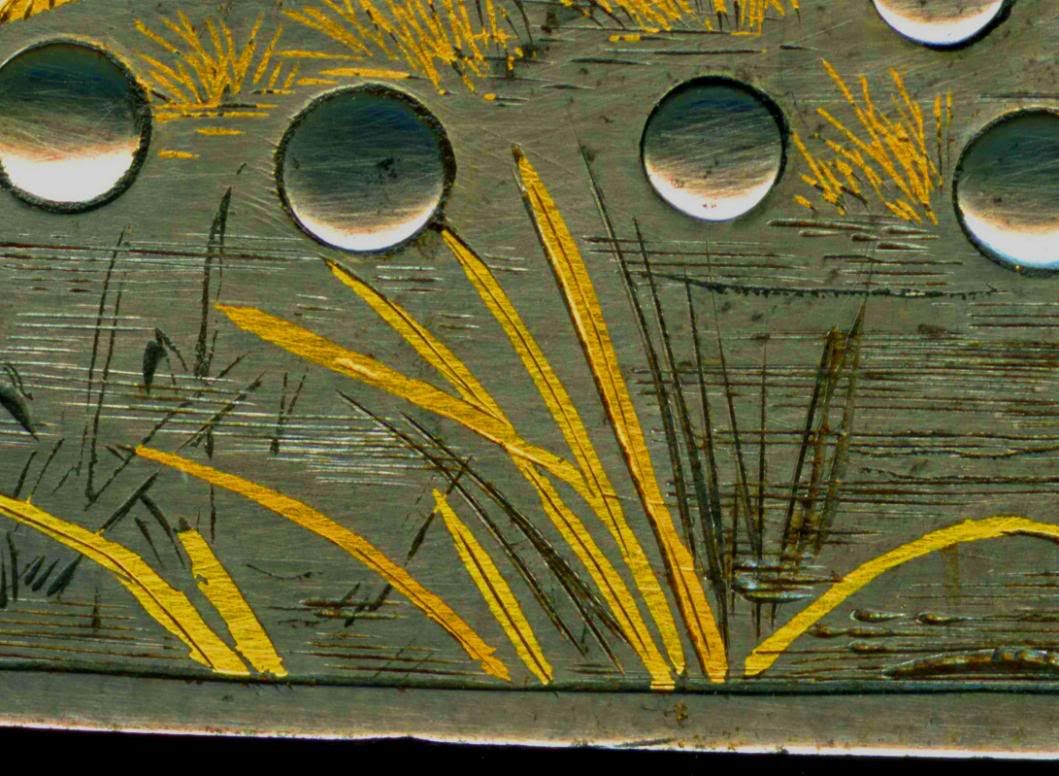
![]()
![]()
![]()
|
Barry, thanks for the added info. I wasn't trying to denegrate Ken's work but to show there is a consistancy there that it would be interesting to persue. I would like to know just what the cause of inlay failure is so as to avoid. Nothing that I have engraved is likely to ever have the usage of this piece so I will never know if my inlays can stand up to such wear and tear. All I know is they stand up really well to 30 years in the safe. When I said "excellent job" I was also refering to this thread. It is interesting and very educational and it would be nice to see more of this sort of thing. Guess I need to learn to post some photos to the web so I can participate also. S
Sam Welch
12/1/2005 4:36:36 PM

![]()
![]()
![]()
|
Thanks Sam. I have never seen an inlay installation done better than yours, I think you can be confident they will be there a while.I remember reading" Lay not up your treasures upon earth where moths and rust doth corrupt" so I guess they will all be piles of rust , or crushed into Nuetrons in a black hole someday. But in the meantime, I think corrosion is the culprit 99% of the time. When rust expands, there is only one thing for the inlay to do, and that is to come out. On a steel boat I think they use a copper plug somewhere, and through galvanic action, the copper oxidizes first, I think. maybe someone can tell me if that is correct. Perhaps we should all install a copper plug on the gun somewhere, hehe. I have fixed several of these and there is always rust behind them. Thanks again for the great comments Sam, Barry
P>S> here is the Lynton side where he used yellow and green also.
Barry Lee Hands
12/1/2005 5:03:52 PM
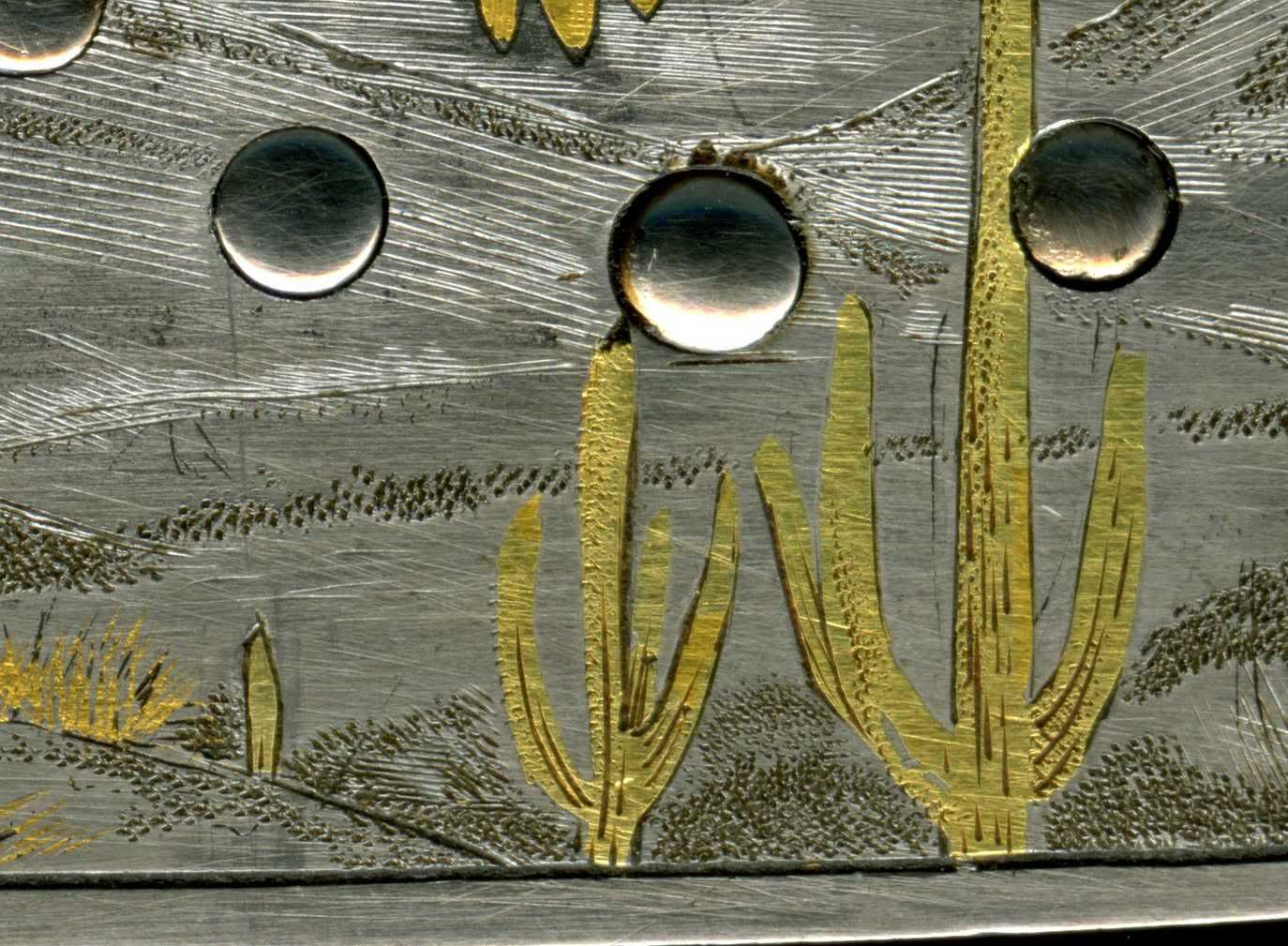
![]()
![]()
![]()
|
Respond |
Back to Forum
|
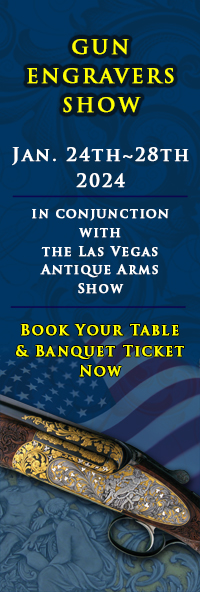
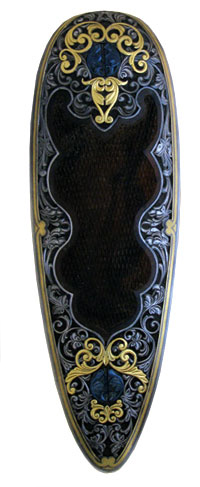
|