Wonderfully clean cutting Barry! |
Barry
Great work done with remarkable speed. I'm just a newbie at metal engraving but not new to the arts. And I really can appreciate a true artist.
I'm particularly taken by your main outlines around the leaf and scroll patterns. You cut them with what I consider a jewelers' "bright cut". Is this the proper name for this style? Do you use a standard square graver? By the way, what brands and types of gravers do you recommend? I'm still searching for the best gravers that can really hold a tip in the hands of a learner. Actualy, I'm really not sure how often one should need to sharpen a graver. Working in gun metal or knife handles (brass or milder steels) what tip life should I expect? Your imput would be greatly appreciated.
Thanks & Merry Christmas!
Mark Sedlak
Mark Sedlak
12/19/2005 10:50:03 PM

![]()
![]()
![]()
|
Mark..Try Steve Lindsay's Carbalt graver...www.airgraver.com.
They seem to hold up well. I used to use old hacksaw blades, the ones they used in machine shops, and now I use the Carbalt. Anything Steve comes up with is well thought out..Hope this will help you.
Yours truly,
JJ Roberts-Manassas, VA
JJ Roberts
12/20/2005 9:41:05 AM

![]()
![]()
![]()
|
Graver theory
This is what I call a 110 degree single point. A 90 degree single point is often called a square, which is simply the shape of the blank. All tools are single points, or two or more single points together. A square being two single points joined on one plane, a liner being many side by side, an onglette a single point with radiused side angles and a tall shank.
I used to make all my tools from 1/8 momax that I got from ray viramontez, I love the stuff. If anyone knows where to get some , please let me know. Lately I use glensteel square blanks for anything that needs to flex, or precious metals cuz gold does not stick to it. I use carbide from ngraver or glendo for 110 and 70 degree single point tools. I do not like the X7 much, it is softer than carbide, and almost as brittle. I have never used the Lindsay steel, I wish he would send me some to try, hehe.
That scroll was cut with a GRS carbide blank with a 110 degree shank , a 55 degree face and a small curved belly, somewhere in the 15-17 degree range I imagine. I cut all of it including the shading with that tool in that, my simplest, style. I call it " Empire style" because the earliest guns I have seen with it are in the Liege museum and were made in that area in the early 19th century. You can also see it in the Uffizi, the Vatican and even Athens dating back a couple of thousand years, but the earliest I have seen it on guns are 19th century. Lynton McKenzie was influenced by this style.
There are many other tools I use for other styles, but I like Empire because it only takes one tool, which makes sharpening easier, and my bench neater. BLH
Barry Lee Hands
12/20/2005 11:01:49 AM
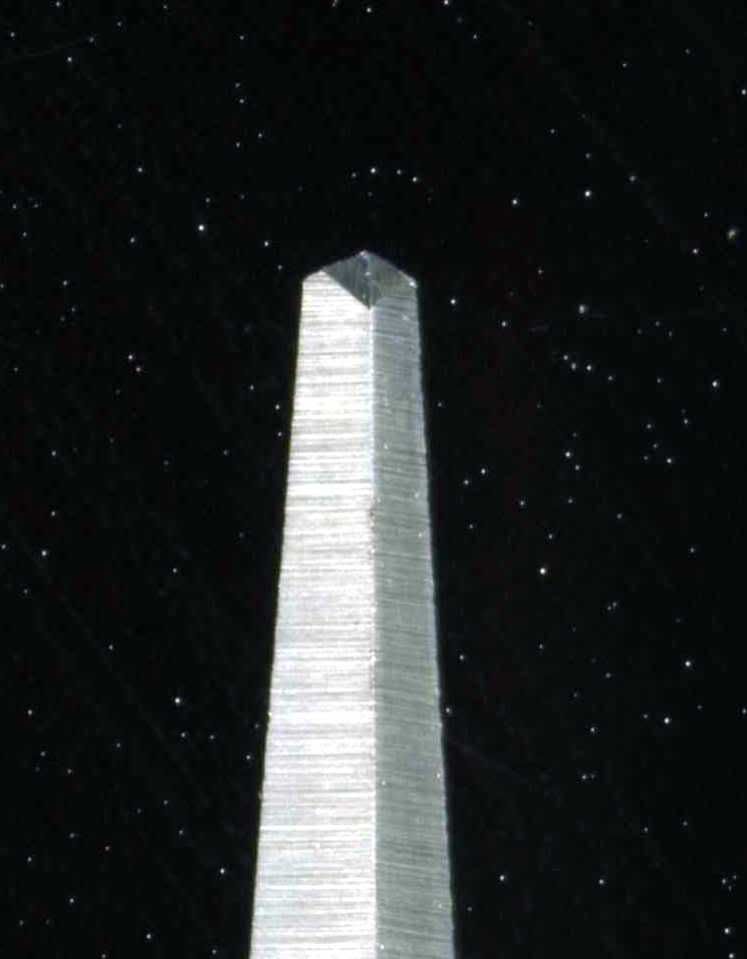
![]()
![]()
![]()
|
As to the brightness of the cuts I use a 1/8 Rod shown in the pic to sharpen the belly on my diamond stone, then I do the same procesws on a ceramic ston with diamond spray applied. I have atwo power hones, but use the for facing and shaping the shanks mainly. Then I may use a piece of leather with diamond spray to polish the belly, Mike Dubber showed me that technique. He makes some of the brightest cleanest cuts I have seen. He is good at all those little engraverish bright cuts and fourishes.
Barry Lee Hands
12/20/2005 11:08:05 AM
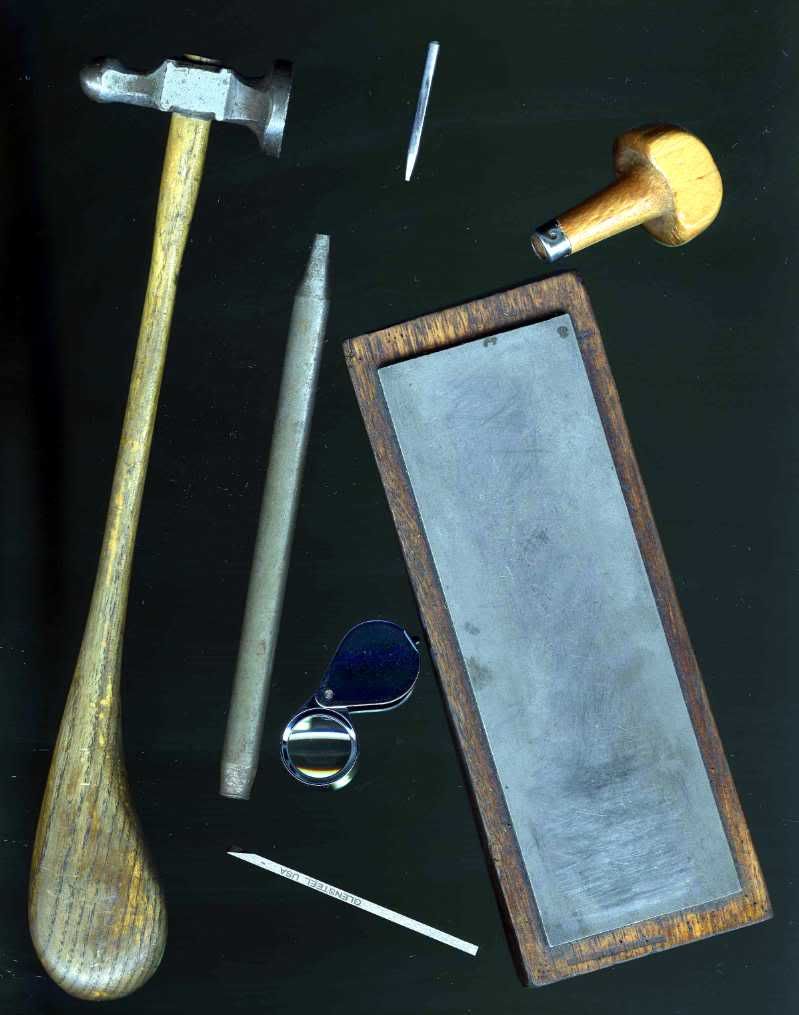
![]()
![]()
![]()
|
here's another for you, this is a rib from a single shot Rifle. It is all done by etching and punching.
Barry Lee Hands
12/20/2005 6:54:52 PM

![]()
![]()
![]()
|
Mark, to answer your bright cut question, that term usually is applied to a wide bright cut made with a flat. And to the other, my 110 single points last about half a day. B
Barry Lee Hands
12/21/2005 1:14:29 AM

![]()
![]()
![]()
|
Barry,
Thanks for the info. As usual, the more I learn, the more questions come up! The close-up photo of the graver confused me a bit. Do you grind the taper seen in the picture on all four sides of the tool, or just the "top" two sides, so as not to disturb the pre-set 110 degrees? And what did you mean by "I use the 1/8 inch rod to sharpen the belly on my diamond stone"? Do you rest the graver on the rod which is laying on the stone to get the 15-17 degree angle? I never realized how much of the graver blank you guys reduced before you have a working tip. I hate to be a pain in the butt, but can you send some pics of the graver from other angles? I like the concept of using one graver for the majority of the work. And by the way, I have to resharpen every 15-20 mins.! So I'm abusing the tool somehow. So I've got a "lot of learnin'" to do.
Thanks again,
Mark
Mark Sedlak
12/21/2005 12:56:31 PM

![]()
![]()
![]()
|
Mark, I use the method passed down to me from the " Master" engravers who taught me at Gist engravers in Vacaville Ca. It was taught to them by older engravers, who had it passed down to them etc, and is the same technique McKenzie uses in his vid. As you guessed, I rest the rod on the stone, and use it as a crutch. It is the fastest . simplest, most accurate method I know to put a belly on a tool. If your tool breaks a lot it is one of two things, you are turning the work while the tool is not cutting, wich causes severe torsional stress on the tiny, tiny bit of tool in the metal, or you are sharpening incorrectly , or both.
The best way to learn to sharpen tools is to cut by hand with no power. This is because a power tool will drive any piece of tool steel through another softer steel. If your tool will cut without power, it is properly sharpened, and will last much longer, because it IS properly sharpened.
Lathe bit sharpening is Identical to graver sharpening except the back rake angle is much larger because it is hand held instead of in a tool post.
Just cut a lot and it will come.
Barry Lee Hands
12/21/2005 7:22:47 PM

![]()
![]()
![]()
|
good GRS diagram..
Barry Lee Hands
12/21/2005 7:23:37 PM

![]()
![]()
![]()
|
Try again, hehe
Barry Lee Hands
12/21/2005 7:24:34 PM
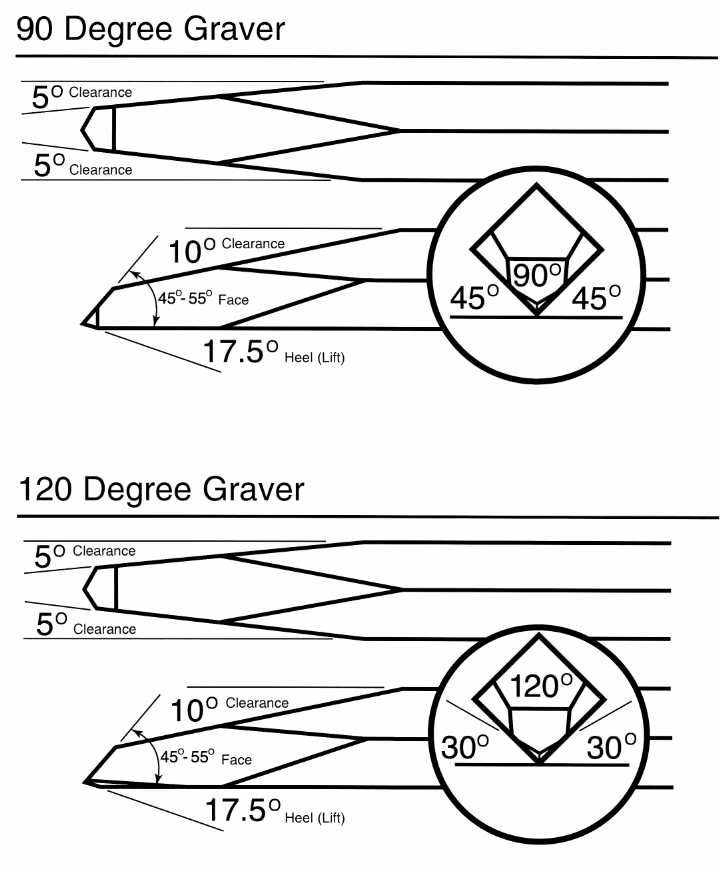
![]()
![]()
![]()
|
Great diagrams! I actualy get it! Now I realize why the photo of the graver threw me, I thought I was looking at the top, not the bottom of the graver. Thanks again for all your help. And yes, I think I am turning the work too fast before the tool can "catch-up" and cut smoothly. As you say, lots of practice needed.
All my best,
Mark
Mark Sedlak
12/22/2005 11:10:45 AM

![]()
![]()
![]()
|
Respond |
Back to Forum
|
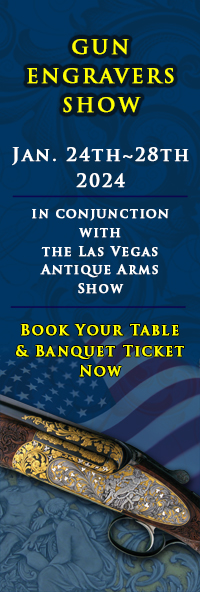
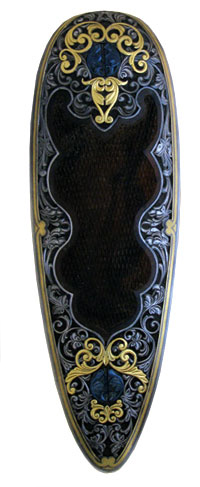
|